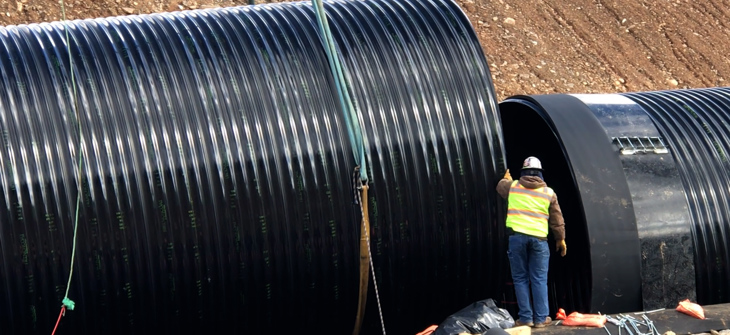
Top Three Pipe Coatings/Materials used in Underground Detention Systems
Corrugated metal pipe (CMP) is the “go-to” material for most stormwater detention and infiltration projects. A wide range of gages, corrugations, and diameters provides engineers flexibility in design not available with other materials. In addition, the industry has developed several pipe coatings and materials to accommodate site-specific durability needs and extend serviced life. It is helpful to the engineer to know what coating and material options are available when designing a CMP detention system for a specific site.
Aluminized Type 2 (AASHTO M274, ASTM A929)
Aluminum-coated type 2 (ALT2) is the most widely used supplemental coating for CMP. It is made from steel coil that has been hot-dipped coated on both sides in commercially pure aluminum alloy, creating a bi-layer duplex coating. This process gives the material the durability of aluminum with the high yield strength properties of steel in highly corrosive environments.
Aluminum is a reactive metal, but the unique type 2 coating develops a passive aluminum oxide coating or film that protects the inner steel from corrosion in many environments. Over 50 years of field testing confirm that Aluminized Steel Type 2 (ALT2) corrugated steel pipe offers a minimum 75-year service life in the environmental ranges of pH 5-9 with resistivity as low as 1,500 ohm-cm.
Polymer Coated Pipe (AASHTO M246, ASTM A742, ASTM A849)
Polymer-coated pipe provides the most extended service life of any metal material used in underground detention systems. First introduced in the mid-1970s, polymer coated corrugated steel pipe is manufactured from a galvanized steel coil coated with a protective ethylene-acrylic film, which protects against abrasion and corrosion. This tough film serves as a protective barrier - resisting corrosion from acids, salts and alkalis found at some sites. According to a 2012 study performed by the National Corrugated Steel Pipe Association (NCSPA), polymer-coated CMP provides a 100-year service life in most environmental conditions.
Aluminum Alloy Pipe (AASHTO M197 ASTM B744)
The corrosion resistance of aluminum alloy pipe is achieved by a special aluminum clad. The rugged core alloy 3004- (H32 or H34) is highly corrosion resistant. But aluminum culvert coil is also clad on both sides with alloy 7072, which is anodic to the core alloy— protecting it both physically and electrochemically against corrosion. These aluminum alloys have a proven history of excellent corrosion resistance due to a thin, tenacious, inert oxide barrier that forms on the metal surface when exposed to air. This rugged, tightly adhering oxide barrier cannot be easily removed. If damaged or affected by an aggressive environment, the oxide barrier reforms. This is referred to as a “self-healing” effect. The oxide barrier appears on the pipe surface as a grayish-white coating that will build up over time.
Aluminum Alloy Pipe CMP is ideal for stormwater detention systems that must withstand alkali soils and erosive environments. State and federal agencies have conducted service-life expectancy studies on installed aluminum drainage products since the early 1960s. Sixteen gauge (0.060”) corrugated aluminum pipe provides a predictable service life of 75+ years in the recommended soil/water environments with a pH range of 4.0 to 9.0 and resistivity of 500 ohm-cm or greater.
If you need guidance on what pipe material to use on a particular sight, your local Contech Stormwater Consultant or Sales Engineer will be happy to review the site details and provide a recommendation.