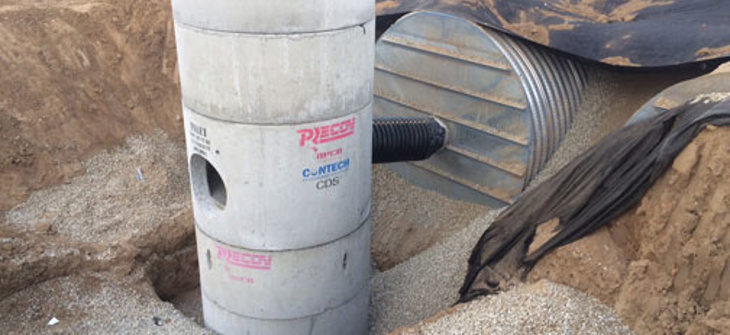
How to Size a Hydrodynamic Separator
Hydrodynamic Separators (HDS) have been used in the stormwater industry for over 20 years. They are effective at removing TSS, hydrocarbons, and trash and debris from stormwater runoff and are often used for standalone treatment or pretreatment to filtration, detention, infiltration and rainwater harvesting system. With the varied applications for HDS units comes a multitude of sizing options.
Sizing and selecting the right HDS unit for your project can be challenging and confusing, here are some thoughts to guide you in the sizing process.
Always start by checking the local regulations
In many cases local or state regulations will dictate how to size a HDS unit and even provide a list of what products are approved for use. Two examples of state regulations are Washington and New Jersey. Both programs dictate the required removal targets in terms of removal percentage and particle size. Both programs also provide a list of approved products making it a simple process for anyone to size an HDS unit.
There are no regulatory requirements, now what?
1. Define the removal targets.
- Identify which pollutant(s) need to be removed and their target removal percentage? Not all HDS units are created equal and some are better at removing certain pollutants such as TSS, trash, and hydrocarbons than others.
2. Assess site limitations.
- Identify the footprint and depth constraints where the HDS unit is to be located. These attributes may sway the designer toward a smaller footprint manhole treatment unit or if utilities, bedrock or groundwater are in the way, a shallower vault system may be more appropriate.
3. Identify the treatment and peak flow rates
- Identify the treatment flow rate or annual removal target to select the appropriate model size needed to achieve the removal targets.
- Identify the maximum flow rate (peak flow rate) that could enter the HDS unit. Some HDS units incorporate an internal bypass which allows flows above the treatment flow to be internally bypassed in the HDS unit. If a HDS unit does not incorporate an internal bypass weir the system should be placed offline.
4.Evaluate product features
- Choose a product that has features that help meet your project goals. Special product features such as screens to target and retain trash or baffles to capture oil and grease can ease the selection process.
- Some systems can be placed strategically on the site to eliminate the number of structures that are required and save time and money. Examples include multiple inlet HDS units to eliminate a junction structure, grate inlet HDS units to eliminate inlet structures and internal bypass systems to eliminate the need for a separate bypass structure.
- Assess the maintenance access situation. Not only is important to have access to get a vactor truck to the unit, there should also be clear access in the unit to effectively remove the pollutants. Without proper access maintenance can become expensive, or worse, impossible.
Ultimately it comes down to performance. When comparing HDS units, look at third-party testing data along with product features to choose the best option for the site. When comparing systems, equivalent requirements need to be considered.