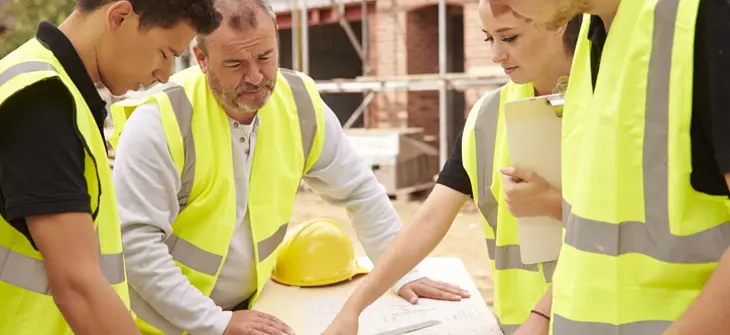
Why Hold a Pre-Construction Meeting?
Whether you are involved with the design, installation or the manufacture of stormwater BMP’s, the key ingredient to a successful project is communication. Poor communication, or worse, no communication, can be a project's downfall. The best way to ensure excellent project communication is to have a pre-construction meeting.
But why have a preconstruction meeting for stormwater BMP’s? They are not that complicated, right? It’s fair to say that all stakeholders (owner, engineer, contractor and manufacturer) want a successful project. Taking the time a week prior to installation to cover key items will save time, and money, by recognizing and mitigating any issues before they arise.
When should the preconstruction meeting take place?
It’s best to hold the actual meeting no more than a week prior to the start of the actual installation. This way the information is still fresh in everyone's minds. This time frame also allows all the primary players time to adjust to new and changing information.
Generally speaking, a preconstruction meeting should take place under the following conditions:
1. If it’s the engineers first time designing the BMP or the contractors first time installing the BMP
2. If the BMP is new to the geographic area.
3. If the project has joint tightness requirements.
4. If you are installing a detention system and the pipe material requires any special backfill or other installation techniques i.e. flowable fill, thrust blocks, backfill type, etc
5. If the project’s BMP has any post-installation requirements in order to be placed online.
Many of these items should be also covered in the design phase of the project. This makes sure that the owner and engineer feel comfortable using and designing the BMP and the contractor has the information to properly bid the installation. However, holding the preconstruction meeting assures that any items which have inadvertently slipped through the cracks are addressed early in the construction phase. This minimizes wasted head-scratching time on site.
Who should attend the preconstruction meeting?
The key players are the project owner, engineers, contractor and BMP supplier. Other entities to be considered are the QA/QC engineer, geotechnical engineer, backfill supplier and any affected sub-contractors. Ideally, the attendees from each entity will be:
Engineer(s):
• Project Manager
• Design Engineer, if different from the Project Manager
• QA/QC or Site Monitor
Contractor
• Project Manager
• Estimator, if different from the Project Manager
• Site Superintendent
• Crew Superintendent
BMP Supplier
• Technical Representative
• Sales person, if different from the Technical Representative
Every company uses different titles for different roles. The primary concern is to make sure that all the required information makes its way to all the people who affect the pipe’s successful installation.
What should be discussed?
The meeting is generally led by the BMP supplier because they will discuss their recommendations based on their experience with the specified system(s). That being said, the best preconstruction meetings are open forums rather than presentations. Everyone should feel free to ask questions, bring unforeseen issues to light, and add input based from their previous experiences. Each BMP preconstruction meeting should review the following at a minimum:
Submittal package and drawing review
• Many installations require items like manholes, manhole lids, ladders, etc. Review what the BMP supplier is supplying and what they are not.
• Some BMP manufacturers provide on-site QA/QC and installation support, others do not. Who is on site ensuring a successful installation?
BMP material delivery timeframes
• Supplier’s availability should be reconciled with the contractor’s on-site requirements.
• Which pieces needed on-site first?
• How is it being delivered (number and type of delivery vehicle, etc.)?
Installation
• What material will the supplier provide and what material is the responsibility of the installation contractor?
• What type of lifting devices are needed to offload and install the BMP and who will be supplying these?
• What is the overall weight of the heaviest piece and what equipment will be used to handle this?
• Will any components need to be installed after the installation? If so, who will be installing these? What role, if any, does the contractor play in this?
• Are there any special backfilling requirements?
• What post-installation requirements are needed to place the BMP online? Who will be responsible for these?
Much of this information will have been transferred during the bidding phase of the project, and it may seem that getting together to review it is not required. Considerations like permitting, material availability, weather, miscommunication, and other projects can easily change many project aspects. Identifying these discrepancies early is the key to effectively addressing them.
A successful preconstruction meeting will help bring all the project stakeholders together to discuss how to successfully complete the project. It will identify any discrepancies between each stakeholder early enough to address them effectively and economically. It also provides a map of the stakeholders should a later issue on the job site arise. In the end, early communication is always the key to a successful project.