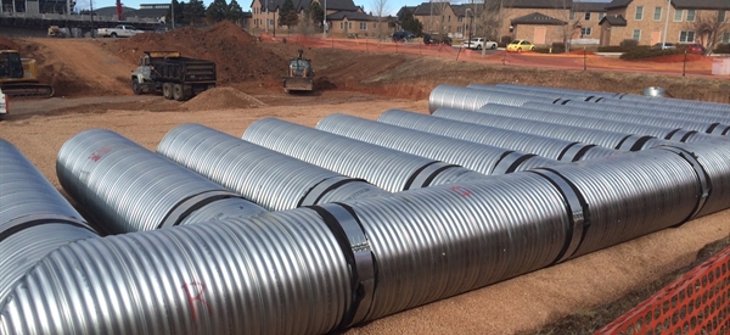
Designing CMP Detention Systems: Part Two – Cost Effective Design and Layout
Cost-Effective Design and Layout Tips for CMP Detention Systems
In part one of this three part series we looked at the value of underground detention systems. In part two, we will provide insight in designing efficient and cost effective systems.
Regarding minimizing costs, the three most importing goals should be to shrink the footprint of the system by maximizing the storage volume within a given area, eliminate unnecessary welding/fabrication, and eliminate unnecessary structures.
Shrinking the Footprint
The goal of any CMP detention system should be to maximize the vertical space available to minimize the overall footprint, to reduce material, excavation, and backfill costs. To do this we recommend using the largest diameter pipe possible.
Increasing the depth of a CMP infiltration system allows for a smaller footprint while storing the same amount of water. For example, doubling the diameter of pipe yields four times as much storage volume per foot in the pipe. This provides significant cost savings per cubic foot of storage. Also, more vertical storage space means a smaller footprint equating to less excavation, less backfill and lower project costs. Consider the following example:
System 1 is made from 36” diameter pipe that provides 5,005 cubic feet of storage. System 2 is made from 60” diameter pipe that provides the same 5,005 cubic feet of storage. Both systems provide the same amount of storage, but System 2 is the most economical design as it reduces material costs, fabrication costs, excavation, and backfill costs. Having fewer runs of pipe will cut down on the number of welds and special fabrication requirements. Having fewer welds will also cut down on lead times. Lastly, System 2 has a footprint that is 1,300 square feet smaller than System 1, reducing excavation and backfill costs. The only instance, where System 2 may not be feasible, is when you do not have the available depth for the larger diameter pipe.
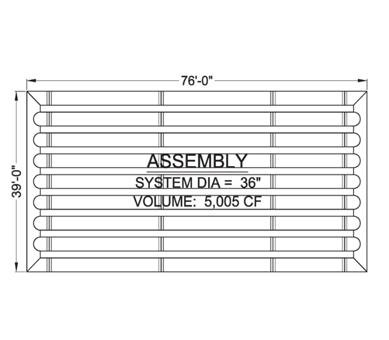
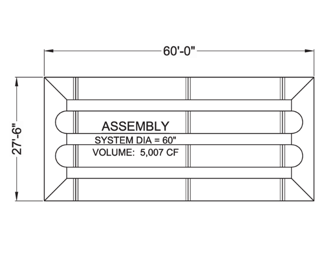
Eliminating Unnecessary Welds
The rule of thumb is to use as much straight pipe as possible to reduce the number of tees and elbows in your design. Doing so will result in a more cost effective and efficient design, and will also reduce lead time. In the example below, both systems are designed with 72” diameter pipe and roughly the same storage volume. System 1 uses only two elbows and one tee and will be much more cost effective than System Two that uses four elbows and six tees.
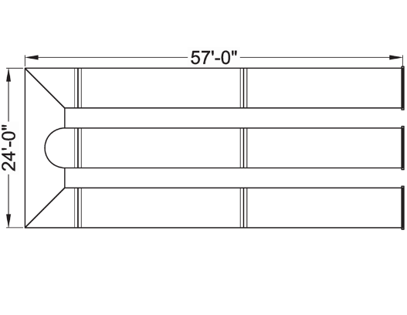
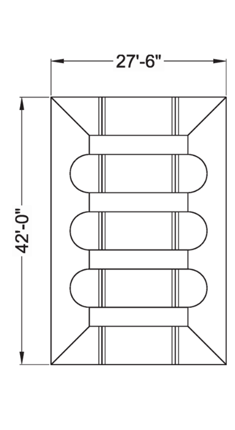
Eliminating Unnecessary Structures
Costs can also be reduced by eliminating concrete structures such as catch basins and outlet control structures by incorporating them into the CMP system. For example, a riser can be added to a system in the low point of a parking lot with a grated inlet to eliminate a concrete catch basin. Internal weir plates and multiple external outlet stubs can often be used to eliminate a separate concrete outlet control structure downstream. Such designs may seem a bit unusual for an engineer that is used to designing with concrete structures. Contech’s team of stormwater design engineers have experience in this and can assist with the routing designs of CMP detention systems.
CMP’s unique ability for custom fabrication and layout versatility sets the material apart from other systems like chambers and concrete vaults. It allows engineers to be creative and to design customized systems to meet site specific conditions that will truly benefit their clients in terms of functionality and reduces costs.
In our third and final part of our series we look at design red flags.