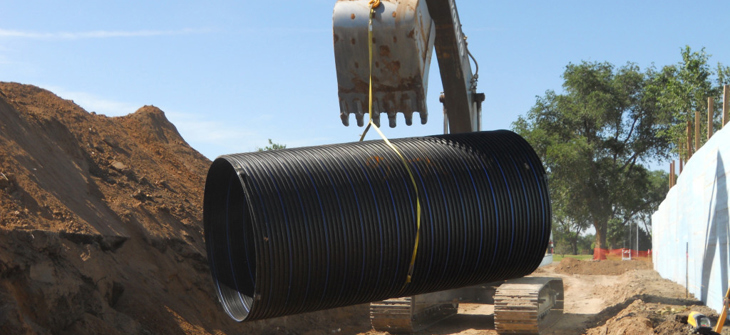
Things to Consider for Large Diameter Gravity Flow Thermoplastic Sewers | Part 1
The need for large and ultra-large sanitary sewers is growing as community populations and conveyance flow requirements increase. Many expert studies have estimated that the sanitary sewer market will grow at a 6% compound annual growth rate (CAGR) in the coming years. With this growth, alternative materials, such as thermoplastics, are being designed more frequently due to the corrosive sanitary sewer environment. When discussing designing large diameter sanitary, it should first be noted that there are differences between small diameter collections systems (4” – 15”) versus the large diameter world of interceptors and trunk lines (36” – 120”). Typically, the larger diameters tend to have far less directional changes and lateral connections. Also, interceptors tend to have deeper heights-of-cover in gravity flow applications. Many interceptors are designed to flow 50% to 70% full, with minimal slope, deep covers, and within groundwater (requiring dewatering installation). It is also not unusual for new interceptors/trunks to be miles of pipe using several diameters.
When looking to develop thermoplastic pipe specifications, engineers might want to consider these areas of concern: hydraulics, watertightness, deep covers, and connections. We’ll take a look at the first two in detail.
Hydraulics
Most agencies adhere to the Manning’s “n” value of 0.012. This meaurement is based on decades of concrete pipe design, and it should be noted that there are thermoplastic materials that do provide a roughness coefficient as low as 0.009 (e.g. PVC materials). Many engineers agree with this and use this as a safety factor, but still model using the 0.012 value. More important to understand, almost all thermoplastics are tested at the same testing hydraulic flume under laboratory conditions. It is important that engineers know that not all thermoplastics perform the same, hydraulically, once they have been installed and are loaded in ring compression. Some of the lower modulus materials (e.g. visco-elastic such as non-reinforced polypropylene) can incur inner wall buckling due to circumferential shorting and thin inner walls. This inner wall buckling can raise the installed Manning’s “n” value from 0.012 to 0.017 or higher, reducing the flow upwards of 40%. There are several HDPE materials that have thicker inner walls, as well as steel reinforced HDPE (e.g. SRPE) that do not have inner wall buckling due to the use of high modulus steel for structural performance.
Watertightness
Maintaining watertight joints and connections is very important in this environment to prevent I&I (inflow/infiltration). Most of the thermoplastic manufacturers advertise watertight bells and spigots meeting the requirements of ASTM D3212. Some have welded connections that eliminate the bell and spigot all together. When looking at specifications, one might again consider the difference in thermoplastics from the standpoint of modulus of elasticity. For decades, PVC materials have been a leader in the thermoplastic sanitary world due to the relative material strength versus a deep and wet environment. Weaker plastics such as non-reinforced HDPE or polypropylene have been used less due to the issues with long-term creep. PVC modulus is four times (4x) that of HDPE, for example, and therefore does not creep under loading. This is important for watertight connections that might have a reinforced bell but not a reinforced spigot. Once installed, the pipe might pass an internalized pressure test that pushes the gasket outward into the reinforced bell, but during the design life of a gravity flow system, the spigot may creep causing leaks in the long-term. Some thermoplastics, such as steel reinforced polyethylene (SRPE), use reinforced bells and spigots to prevent this long term phenomenon from occurring.