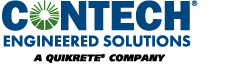
Developing a performance specification for a steel pedestrian bridge is commonly used by specifiers because it allows them to identify the required performance features of the structure while deferring the actual bridge structural design to the bridge manufacturer. It also allows the bridge manufacturer to efficiently design and fabricate a bridge that meets the project needs and specifications while maximizing the efficiencies of their manufacturing equipment and capabilities.
An important performance specification standard is the steel finish. A properly selected finishing system will account for bridge service life, maintenance needs, aesthetics and owner budget. The selection of a steel finish depends on multiple factors, including environment, application, owner experience, owner preference and budget. Future maintenance also needs to be considered in the long-term cost analysis. It’s very important for the decision makers to ask others and themselves the following questions during the selection process:
• What is the bottom chord elevation in relation to the water crossing, vegetation or embankment backfill?
• Is this water course subject to flooding, turbidity or consistent spray?
• Is the structure located in proximity to saltwater or a generally brackish environment?
• Will the use of deicing salts or other maintenance chemicals be part of the regular snow removal or landscape plan? Bridges near schools, commercial zoning, hospitals and other high-traffic areas often require winter maintenance.
• Is the structure installed near a salted roadway, creating a potential for salt spray?
• How is drainage managed on the bridge and at the approaches?
• What are the aesthetic requirements of the project?
• Will the structure be frequently inspected and maintained?
If a finishing system is improperly selected, it can lead to premature corrosion of the steel and thus a shorter structure life. It can also lead to the project being over budget.
Bridges can be built from non-weathering steel or weathering steel. For this article, to differentiate between non-weathering and weathering steel, we have chosen the term “carbon steel” to indicate non-weathering steel. Other common references include “steel” or “black steel.”
Carbon steel. Most steel used in construction is plain carbon steel, and it is susceptible to oxidation (rust) if exposed to the elements without additional protection. The concern with rust is that it reduces the serviceability of a portion or all of a structure through time. In addition, it causes contaminated runoff, staining and a structural-deficiency perception by the public. Plain, uncoated, carbon steel should not be specified unless the structure is to be installed in a climate-controlled area, such as a fully enclosed connector from one building to another that is climate controlled, or in temporary applications. Often carbon steel has some type of finish applied that’s detailed further in this article.
Weathering steel. Weathering steel is often referred to by the genericized trademark COR-TEN or CORTEN Steel and is available in ASTM 709 Gr 50W or QST XX, A588, A847 and A1065 Gr 50W. The “W” in the steel grade denotes that it is weathering steel when the same material is also available in carbon steel. These steels are alloys that were developed to provide an alternative to painting or galvanizing by forming a stable external layer of rust. This exterior layer must be allowed to form initially and remain in place through time for it to provide protection. Maintenance of a weathering steel structure is minimal after the patina has formed. The structure should not be covered in vegetation or organic matter, used near brackish water or around sea spray or atmospheric conditions that will prevent the surface from regularly drying. In addition, if the structure is exposed to deicing chemicals, it should be inspected and washed regularly.
Weathering steel is produced in the same shapes and sizes as carbon steel, making it easy to design and build with. Due to the ease of fabrication with weathering steel and the relatively low maintenance requirements, it’s typically selected as the preferred material for many steel pedestrian, vehicular truss and girder bridges. In addition to the minimal-maintenance advantage, weathering steel does not require coatings, thus offering the most-accelerated construction and least-cost option. Weathering steel can be coated with paint or galvanizing, but the advantages may not equate to reduced maintenance or lifecycle costs.
Stainless steel. Stainless steel has greater corrosion-resistance properties than weathering steel and is the preferred material for many applications. It’s widely used in handrails, food-processing facilities and medical equipment. The lack of available structural shapes and increased material and fabrication costs are deterrents to its use in most structural steel applications.
Surface preparation. Preparation is key to the success of a steel coating system. In 2021, the National Association of Corrosion Engineers (NACE) and the Society of Protective Coatings (SSPC) combined to form the Association for Material Protection and Performance (AMPP). This association is interested in all aspects of material protection and coating performance. They have guidelines for surface cleaning from just wiping a structure of manufacturing and fabrication marks to blasting to a near-white finish. The industry refers to these surface profiles with a number, thus SSPC-SP# (profile number). Each profile number qualifies the amount of staining as well as the surface profile or roughness, if required.
In the prefabricated bridge industry, SSPC-SP1 (Wipe Off), SSPC-SP7 (Brush-Off Blast), SSPC-SP6 (Commercial Blast), SSPC-SP10 (Near White Blast) and SSPC-SP16 (Brush-Off Blast of Galvanized Steel) are typically used. These finish specifications are defined and inspectable based on AMPP criteria. This surface preparation standard helps ensure that the coating will perform through time by removing surface coatings and contaminants that could compromise a finish’s ability to properly adhere to the steel. The blast number is not a linear scale, and specifying a higher number does not mean better blast. To determine the required surface preparation, the entire finish system needs to be considered, and the manufacturer’s Product Data Sheet (PDS) for the coating system should be referenced to determine the surface preparation criteria.
The American Institute of Steel Construction (AISC) developed a criterion for Architecturally Exposed Structural Steel (AESS). The AESS category system has a scale of how visible the exposed steel elements of fabrication will be to the public and, based on those criteria, establishes an acceptable category for those portions of the structure. These criteria set forth acceptable levels of weld visibility and fabrication/manufacturing markings that can show through in the finished work. Prior to specifying AESS, the intent of the specification and the cost associated with the work should be thoughtfully researched. In addition, sample pieces of work should be produced and agreed upon by the fabricator, painter, inspection agencies, architects and owners. One of these samples should be kept at each: the fabricator, painter and project location to act as a reference for the acceptance of the finished work. Specifying AESS adds to the project lead time and significantly to the cost of fabrication and finishing.
Numerous systems are available to extend the life of a steel structure. Some need to be applied as part of the original construction, while others can be applied after the bridge is installed or as part of a regular maintenance program. Typical finish systems in the industry are galvanizing, metalizing, painting or a duplex system. We will explore each of these systems as well as review their benefits and additional considerations.
Paint.Paint is a very common barrier to use for protecting steel from the elements. For carbon steel bridges, typically a three-coat paint system is used. The first layer is a zinc-rich primer applied over a properly prepared surface, typically blasted and washed. This primer coat has high adhesion properties to bond the paint to the bare steel. The middle coat is a high-solids full-coverage coat to ensure all the primer and sharp edges have sufficient coverage as well as promote adhesion with the top coat. The top coat is typically a two-part paint that can be color tinted as requested by the owner.
The paint process is dependent on atmospheric conditions and should be performed in a climate-controlled facility. AISC 420-10 Shop Application of Complex Protective Coating Systems is the standard for evaluating paint-application facilities. Facilities that meet the criteria are given a Complex Coating Endorsements as part of their AISC accreditation. The endorsements are based on the level of enclosure the paint facility has: Enclosed, Covered and Open.
The Northeast Protective Coating Committee (NEPCOAT) was formed to establish acceptance and testing criteria on highway bridges. Although initially a regional committee, states across the country have started to adopt it as their standard. The NEPCOAT has a list of approved two- and three-coat organic and inorganic paint systems. In addition to following NEPCOAT guidelines, some agencies require samples of the paint to be sent in for testing.
When selecting a paint system, it’s best to identify the level of performance the owner wants from the paint and then find a reputable paint system that meets those specifications and criteria. Top-coat samples are available in what the industry calls a “draw down.” These should be reviewed and approved by the owner prior to ordering the paint. In some cases, a full-size mockup may be required for approval.
Benefits:
The main advantage of a painted bridge is that the owner or architect can select the colors of the bridge to align with other aesthetic features of the project. In addition, paint can be applied in the shop or field. Also, the paint system performance is not affected by the repair and touch-up process, as the method to successfully perform this work is well documented.
Considerations:
Paint systems can be damaged in shipping or onsite by impact or vandalism. In addition, paint has a limited life expectancy and will need to be reapplied to maintain the expected level of protection and aesthetics. Periodic touch-up painting is commonly required, and the amount of time until a full recoating is needed depends on the factors previously mentioned. Some paint colors are subject to fading in just a few years and, in some cases, touch-up areas need to be expanded so they are not distinguishable. Coordinating with the industrial paint supplier is recommended prior to color selection to understand the paint’s performance and recoat characteristics.
Galvanizing. Galvanizing is the process of dipping steel parts in a series of baths, the most notable a kettle of molten zinc. The steel assembly is left in the zinc bath until the base metal has reached the same temperature as the zinc bath. The finished product is a multi-layered protective alloy of zinc that has chemically bonded to the steel. In addition to the surface protection, all surfaces of the part are covered with zinc, and the coating will act as sacrificial anode to reduce the oxidization in the steel assembly.
The ASTM specification for Hot Dipped Galvanizing is ASTM A123, which is used by the industry to ensure that sufficient coating thickness is attained on all parts. Some galvanizers use a quenching bath at the end of the process to cool the material. This process can affect the adhesion if additional coatings are to be applied. It is best to discuss the specific application for the galvanized element with the galvanizer prior to having the work completed to confirm the correct process for the application.
Benefits:
The primary advantage of galvanized steel is its ability to extend the useful life of a steel structure with minimal maintenance. A chemical reaction that occurs in the kettle results in the zinc becoming a part of the steel as opposed to just a surface coating. It also provides uniform protection across all surfaces of the steel, even corners, edges and inside hollow sections, which would otherwise be susceptible to thin application with other coating options. Due to all these advantages, many galvanizers will offer extended warranties against corrosion. The American Galvanizing Association (AGA) is an excellent reference for galvanizing information, and it states that a 70-year life is a reasonable expectation for galvanized structural steel.
Considerations:
Despite all the advantages galvanizing can offer, there are other factors that need to be weighed as well. Some feel it offers an “industrial” and “inconsistent” color appearance, making it less desirable for some applications. There’s also an added cost with this application, which is generally priced on a cost-per-pound basis. If the steel element is small enough, it can be dipped one time, which is preferred. If the steel assembly exceeds the size of the dipping tank, then it will need to be progressively dipped, which means that it’s dipped, rotated and then dipped again in the opposite direction. This progressive dipping will generally result in a cost per pound that’s approximately 40% to 50% greater, depending on the galvanizer. It also will result in a visible dip-line.
The process requires vent holes in all hollow sections and areas of overlap. For this reason, structures using HSS members (tubes) will leave the galvanizing location looking like shiny Swiss cheese. With thoughtful placement of the vent holes and a coordinated dipping plan among the designer, fabricator and galvanizer, these holes can be minimized but not eliminated. To cover these vent areas, tube caps or zinc plugs may be installed after the galvanizing process and prior to the first coat of paint.
In addition to these items, there often are areas where the galvanizing doesn’t flow smoothly from the structure while it’s being removed from the kettle. These areas can be sanded down to a minimum zinc thickness, but they may still be visible and compromise the overall finish.
Metallizing. This process involves a sprayed application of molten zinc or aluminum. The material is melted with either an electrode or flame and then sprayed on the prepared steel assembly to the required thickness. This process can be performed in a shop setting as well as a field application. Think of it as a hot-dipped galvanized coating that’s applied like a paint.
Benefits:
There are several advantages to this technology that have played a role in its growing popularity. First and foremost, since the process is very similar to painting, it can be used in situations where a steel assembly is too large to immerse in a kettle or breaking it down into smaller sections is not preferred. Also, many companies that provide this service have mobile field operations, making this technology ideal for situations that require the extension of service life of an existing structure through field application. Several DOTs have adopted metallizing as the preferred coating technology to enhance corrosion resistance and have begun specifying it on their projects. The coating can be built up in multiple coats to get the required thickness, but the coating does not become part of the steel material such as in the hot-dipped galvanizing process.
Considerations:
Some drawbacks specifiers need to consider are cost and availability. Every project is different, and sometimes the specification of a metallized bridge can be advantageous over that of a galvanized bridge, especially if the configuration is such that galvanizing would require knocking the structure down into multiple parts and pieces to immerse it in the kettle, then re-assembling it either in the shop prior to delivery or in the field by the contractor. If that’s not the case, since the actual vendor cost for metallization often exceeds that of galvanization, this option will frequently be more costly. Since it’s a relatively new technology, vendors are limited, and the lead time can be significant, making it problematic on accelerated bridge projects.
In terms of quality, since the steel substrate does not become heated to very high temperatures, the risk of distortion is much lower than that of galvanizing. However, it’s important to note that if a structure is built primarily out of hollow structural sections (HSS), like many prefabricated steel pedestrian bridges, then the inside of the HSS will not be coated since the metallizing process involves a spray application. This is different than galvanization, which involves the immersion of steel frames into a kettle, allowing all surfaces (inside and outside) to be coated.
It’s recommended that the metallized surface be top coated as further protection. Often it’s a clear coat, but occasionally it will be painted, depending on the specifications and application. Both add cost to the project.
Duplex systems. Applying a painted finish over a metallized or galvanized finish is referred to as a duplex coating. This system provides the best of both finish systems. There is additional surface preparation work that will need to be performed after the galvanization process. The scope of that work—to ensure adhesion of the paint—will depend on the galvanizing finishing process used as well as the amount of time that has passed between the galvanizing and the paint application.
Excess galvanizing on a drip line prior to paint preparation (top), and the same truss after preparation and base coat of paint (duplex system, bottom).
Benefits:
A galvanized coating provides a high level of protection to the structure and the aesthetic appeal of a painted structure. Studies have shown that a synergy exists between the two finishes that extends its useful service life even more than the sum of the two independent service lives that galvanized finishes and painted finishes would provide independently.
Considerations:
The galvanized finish is typically considered an industrial finish, but when painted there is an assumption that the finished product will look like a plain painted structure. Instead, all the features indicative of the galvanizing process (vent holes, dip-lines, handling marks, etc.) can be visually magnified with the application of paint over the top. Plugging of the vent holes is possible, but there still may be displeasing aesthetic consequences. The specifier and owner should always be aware of this potential issue when considering a galvanized and painted finish for their project.
Conclusion
The selection of a steel finish system may be one of the most-important decisions a specifier or owner makes in the process of specifying a prefabricated steel bridge. The key factors to consider when selecting a finish coat include the following:
• Application
• Budget
• Desired appearance
• Environment
• Owner maintenance preference and requirements
Steel has been proven to stand the test of time, and there’s no reason to believe that it will not do the same for your next project with proper protection. If attention is given to this consideration, it will ensure that your steel bridge is admired for years to come.
Glossary
Carbon steel: Plain, “non-weathering” steel that generally requires some level of protection by way of a coating system; common types available are ASTM A709 Gr 50, A500 Gr C, A992, A572 Gr 50 and A1085.
Weathering steel: An alloy that was developed to provide an alternative to painting or galvanizing by forming a patina; also known as “high-strength, low-alloy, enhanced atmospheric corrosion-resistant steel”; common types available are ASTM 709 Gr 50W or QST XX, A588, A847 and A1065 Gr 50W.
Stainless steel: Has greater corrosion-resistance properties than weathering steel and is the preferred material for many applications, but lack of available structural shapes and increased material and fabrication costs are deterrents to its use in most structural steel applications.
Patina: A stable external layer of protection that forms on the surface of weathering steel through oxidation following exposure to atmospheric conditions.
AESS: Architecturally Exposed Structural Steel.
Galvanizing: The process of dipping steel parts in a series of baths, the most notable a kettle of molten zinc, which provides a multi-layered protective alloy of zinc that has chemically bonded to the steel.
Metallizing: A process that involves a sprayed application of molten zinc or aluminum.
Duplex system: The application of a painted finish over a metallized or galvanized finish.
Draw down: Sample of a top-coat paint color for review and acceptance by owner prior to painting of steel.
Organizations
AGA: American Galvanizers Association, https://galvanizeit.org
AISC: American Institute of Steel Construction, https://www.aisc.org
AMPP: Association for Materials Protection and Performance, https://www.ampp.org/home
ASTM: American Society for Testing and Materials, https://www.astm.org
NACE: National Association of Corrosion Engineers information can now be found, https://sspc.org
NEPCOAT: Northeast Protective Coating Committee, https://www.nepcoat.org
SSPC: Society of Protective Coatings, https://sspc.org
Click on the button below to start the quiz for this course. Your score will be tabulated while you wait, and you will receive your certificate upon completion if you correctly answer eight or more questions.
Registration on v1-education.com is required to access the quiz. Use the "Sign Up" link in the top right of v1-education.com to register. If you are already registered simply enter your credentials to access the quiz.
The Professional Development Series is a unique opportunity to earn continuing education credit by reading specially focused, sponsored articles in Informed Infrastructure.
If you read the following article, display your understanding of the stated learning objectives, and follow the simple instructions, you can fulfill a portion of your continuing education requirements at no cost to you. This article also is available online at v1-education.com.
At the conclusion of this article, the reader should be able to:
The methods used to protect steel via coatings and the formation of patinas.
How to select the appropriate finish for a steel bridge based on the environment and expected usage characteristics.
The benefits and considerations of different finish systems.
How to identify the cost implications associated with each type of finish.
Click on the button below to start the quiz for this course. Your score will be tabulated while you wait, and you will receive your certificate upon completion if you correctly answer eight or more questions.
Registration on v1-education.com is required to access the quiz. Use the "Sign Up" link in the top right of v1-education.com to register. If you are already registered simply enter your credentials to access the quiz.