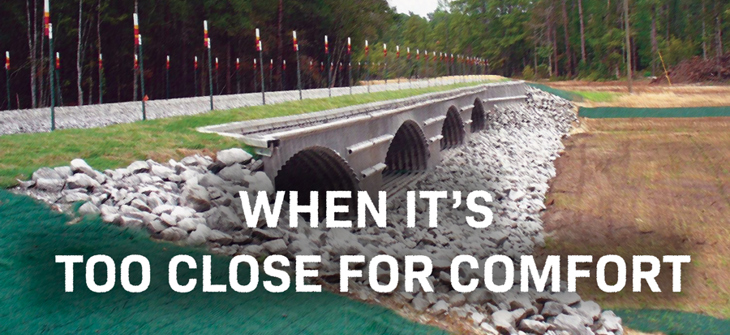
When It's Too Close for Comfort
One of the factors in determining the selection of a structure or structures to convey or store water is whether to use a single cell or multiple cell structures.
The hydraulics and the economy of the solution are primary factors. While a single cell may be the more desirable option, the amount of headroom, or the vertical distance from the invert to the finished grade, may force a multiple cell solution.
There may be a situation where the available width of the footprint is not wide enough to place the structures according to minimum recommended guidelines. National specifications such as AASHTO, AREMA and ASTM, and industry suggestions from the National Corrugated Steel Pipe Association apply to the installation of flexible, corrugated metal pipe and arch structures. Typical wording follows:
Pipe spacing - Proper structure spacing and backfill are crucial in the performance of a system. There needs to be room for the contractor installing the system to get between the structures and work the backfill material for proper compaction. The size of the mobile or tamping equipment might be the determining factor of the separation distance. For arch structures, a common footing may be required between cells, and its size needs to be addressed. The industry standard for spacing is as follows:
- <24” span: use 12” spacing
- 24” to 72” span: use ½ the span of the structure for spacing
- >72” span: use 36” spacing
Assuming that there is enough room to properly place and assemble the structures, the above spacing values might be lessened if specialized backfill material is used. This material needs to be able to move around and under the springline of the structure and under the haunch of a closed bottom shape. The material may be a crushed and angular rock, which requires little compaction or vibration effort, and which may allow for an 18” separation distance.
Similarly, a controlled low strength material (CLSM), slurry cement, or flowable fill might be used. This would allow the separation distance to be reduced to whatever amount is needed to place and maneuver hoses, typically at least 6” to 8”. When using a fluid material, care must be taken to prevent uplift of the structures.
Ultimately, the need is to assure that no voids remain in the area where the specialized material is placed between the structures. Placement of this material must be done in unison with the backfill material outside of the cells, assuring that the load on the pipes is balanced across the width of the system.
Finally, the end treatments need to be looked at. If the ends will require headwalls or end sections, their dimensions may limit the separation distance. Custom metal headwalls and multiple inlet metal end sections are available to help minimize the width.
In conclusion, the footprint width of installed structures might be minimized to fit the site needs.