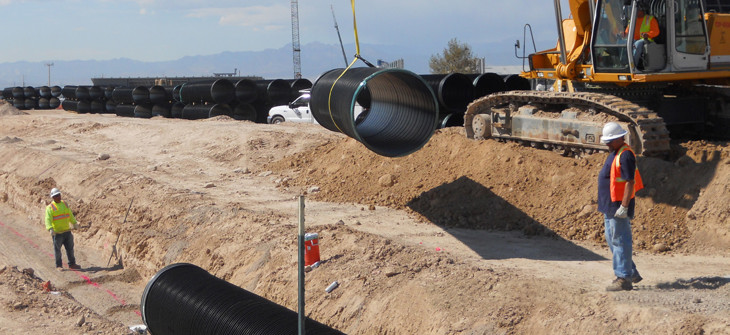
Mastering the Complexities of Large Diameter Sewer System Installation
Handling and installation of large diameter sewer systems demand meticulous attention due to the increased risks associated with their size and weight. From the moment large pipes arrive on site, they must be carefully inspected for any damages, which should be documented before proceeding. The unloading and staging process, determined by the pipe's characteristics such as length, diameter, weight, and the way it's loaded on the truck, must follow the manufacturer's recommendations to prevent any damage post-delivery.
Excavation and trenching are pivotal elements in the installation of large sewer pipes, requiring careful planning to ensure safety. The soil classification influences trenching requirements, which might necessitate an excavation design by a professional engineer. Trench protection strategies include sloping, benching, shielding, bracing, and shoring. Access, egress, and potentially confined space monitoring are critical considerations.
Best practices suggest excavating just ahead of installation to maintain trench stability, while routine monitoring by a competent person is essential for detecting changing conditions.
The control of load and deflection during installation is particularly challenging for large-diameter sewers. The combined weight of the backfill material and any surface live loads contribute to the total load on the pipe. The maximum burial depth is a function of the pipe material, diameter, and its profile wall thickness and material strength.
Excessive loads can cause cracks in rigid pipes, while flexible pipes may experience deflection beyond acceptable limits if design backfill specifications are not adhered to.
Proper installation begins with excavating to the designed foundation or subgrade, followed by placing a bedding layer to support the pipe and distribute the load. After verifying elevation and grade, the pipe is placed and joined in the trench. Large-diameter pipes, varying significantly in weight, pose significant challenges during placement, necessitating careful planning concerning the pipe's length and weight, especially in constrained working areas.
A critical aspect of installation is haunching, backfill, and compaction. The pipeline's interaction with the surrounding soil is vital for bearing loads, making proper soil support and installation essential for satisfactory long-term performance. The haunch zone, extending from the pipe underside to the midpoint, is considered the most crucial factor for controlling deflection. Ensuring uniform circumferential support and load-carrying capability requires workers to manually place haunch zone material or use specified equipment for proper compaction.
Backfill material, typically crushed rock, gravel, or sand-gravel mixtures, is preferred for its long-term structural load bearing properties when compacted to optimal density. Recommended installation practices include maintaining equal backfill heights on each side of the pipe and performing routine compaction testing to ensure material densities are met.
In conclusion, the successful implementation of large diameter sewer systems is predominantly determined by meticulous planning and execution. Pipes are inspected upon delivery, with unloading and staging carefully conducted to prevent damage. Excavation and trenching are performed with safety as a paramount concern, including monitoring trench stability closely during installation. Load and deflection are rigorously controlled through precise installation techniques.
Bedding, haunching, backfill, and compaction are executed with attention to detail, ensuring uniform support and optimal load distribution. The use of proper materials and compaction testing is emphasized to maintain long-term pipe integrity. Throughout the process, safety protocols are strictly adhered to, ensuring the well-being of all personnel involved. The result is a robust sewer system capable of withstanding the demands of its environment, providing reliable service for years to come.