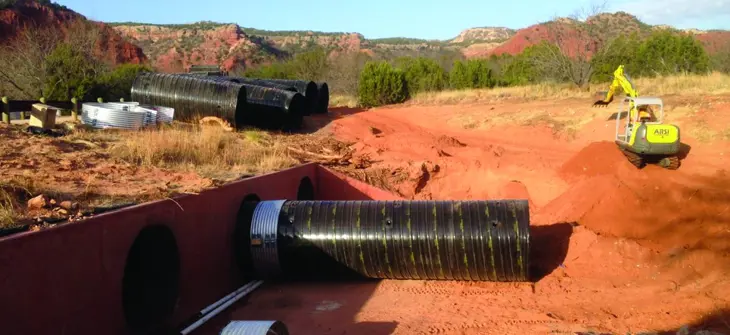
Estimating the Cost of a Reline Project
What to Expect
We are often asked, “How much does a reline project cost?” While this is a straightforward question, the answer depends on multiple factors. Before attempting to provide a cost estimate, it’s important to consider the broader perspective—particularly in comparison to traditional open-cut replacement.
In most cases, segmental sliplining is the most cost-effective reline method unless unique site conditions—such as low traffic volumes, short detour distances, or shallow cover with no utilities—make open-cut replacement a viable alternative. However, generalized cost estimates without accounting for site-specific design and construction constraints can be misleading.
Key Cost Factors
Several variables influence the cost of a reline project, including:
- Condition of the host pipe – Structural integrity and degree of corrosion impact both feasibility and cost.
- Installation plan – Safe and efficient insertion of the new pipe is crucial.
- Size, shape, and fit of the new pipe – Larger or non-standard profiles may increase costs.
- Material type – Different materials have varying costs, durability, and service life considerations.
- Structural design and service life goals – Longevity expectations influence material and engineering requirements.
- Annular grout volume – The amount of grout needed to fill voids around the new pipe affects overall costs.
- Site access – Limited access can complicate installation.
- Appurtenant improvements – Additional site work, such as headwall modifications, can add to costs.
- Traffic control and bypass requirements – Managing roadway closures or flow diversions may be necessary.
- Labor and contractor expertise – Regional wage rates and contractor experience play a role in pricing.
Material Selection Considerations
Segmental sliplining remains the most economical approach, with high-end corrugated metal pipe (CMP) options—such as HEL-COR® Aluminized Steel Type 2, Aluminum, and Polymer-Coated CMP—typically being the least expensive solutions. However, material selection should account for factors like:
- pH and resistivity at low-flow conditions to ensure the chosen material provides the desired service life.
- Hydraulic design analysis, including an evaluation of two-year velocity to determine suitability for expected abrasion levels.
For guidance, the FHWA defines abrasion levels, and Contech’s CMP Design Guidelines provide material selection recommendations.
Additional Reline Material Options
Beyond CMP, Contech offers a variety of reline solutions tailored to different project needs:
- DuroMaxx® SRPE – Cost-effective with superior abrasion and corrosion resistance.
- Tunnel Liner Plate – A hand-placed solution available in Aluminized Type 2 (ALT2) and Aluminum.
- A2™ Liner PVC Pipe – Ideal for trenchless applications.
- ULTRA FLO® Spiral Rib Pipe – Smooth interior for improved hydraulics.
- Structural Plate Solutions – Suitable for large-span applications, including MULTI-PLATE® and BridgeCor®.
Understanding Cost Estimates
While it’s tempting to seek a simple answer, estimating reline costs requires project-specific details. A general rule of thumb suggests that the total installed cost of a reline project ranges from 2.5 to 4 times the cost of the sliplining material. However, this factor can vary—falling as low as 2 times or exceeding 6 times, depending on project complexity.
One advantage of Contech’s reline solutions is that no specialized training or equipment is required, meaning any local utility or underground contractor can successfully perform the work.
Conclusion
Ultimately, the cost of a reline project depends on a variety of site conditions, material choices, and engineering considerations. While segmental sliplining remains the most cost-effective approach in most cases, consulting with a qualified engineer early in the planning process ensures the most accurate cost projections and the best long-term solution.