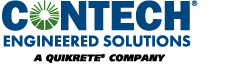
By Darrell Sanders, P.E.
Published: March 2017
Pipe stiffness in the pipe industry is a standard test that is performed on actual pipe samples to determine their ring stiffness. Many product specifications in the pipe industry require a minimum target pipe stiffness be achieved as a requirement for that standard.
Pipe stiffness is generally tested per the requirements of ASTM D2412. Simplistically, this test places a relatively short sample of the pipe barrel between two parallel steel plates. The plates then are drawn together at a prescribed rate, thereby compressing the pipe into an oval geometry. The pipe is deformed until it is compressed to 95% of its original height. The load required to compress the pipe to this dimension is recorded and used to compute the pipe stiffness for the pipe.
This test method describes the size of the pipe samples to be used in the test, the conditioning of the pipe in preparation for the test, the equipment that should be used in the test, the methodology that should be followed during the testing, and how to evaluate the results of the test to determine the reported pipe stiffness. This is a widely followed testing standard that is used for many pipe products—primarily in the plastic pipe industry. The resulting pipe-stiffness values are frequently discussed by engineers within the pipe industry, but sometimes there is some confusion over how stiffness values are computed and how laboratory-measured stiffness relates to field installations.
All index tests must prescribe the conditions that would impact the results of the tests so they are repeatable. For a pipe-stiffness test, some of the important environmental conditions that must be controlled to get repeatable results are the temperature of the test sample and the testing lab, the minimum length of the sample, and the speed at which the test is conducted. If any of these variables change, then the results of the test could be altered significantly.
The difference between laboratory conditions and field conditions can yield significantly different results. For instance, the pipes to be tested per D2412 are to be conditioned in an environment with a temperature of 73 degrees Fahrenheit +/- 4 degrees and tested in a laboratory at the same temperature. However, look at how the measured pipe stiffness of various pipe types varies with temperature:
As the chart shows, pipes made with different materials react differently when tested at higher temperatures than the 73° F used in the laboratory. The polyethylene pipe’s ring stiffness decreased by approximately 49% at 120 degrees, as compared to the laboratory-tested value. Corrugated polypropylene had similar results, where the ring stiffness decreased by approximately 46% at 120 degrees, compared to the laboratory-tested value. The PVC pipe decreased by approximately 23%. Because steel has a significantly higher melt temperature, as compared to thermoplastic products, the corrugated steel pipe only lost about 5.5% of its stiffness, and the steel-reinforced HDPE pipe was in between, with a loss of ring stiffness of about 18.4%. This is significant given that pipe walls can reach 140 degrees or more in the direct sun.
For flexible pipes, short-term deflections are largely induced during the installation process. Flexible pipes can be deformed by a number of different activities during the installation process. Pipe sections are typically bundled and shipped over long distances to get to the jobsite. They then are lifted off the trucks and generally stored somewhere onsite, where they are commonly lifted and handled several more times before they reach the location where they are to be placed.
Although normal lifting and handling doesn’t result in pipe deformations, due to the size and power of the construction equipment used on pipe installations—unintended deformations to the pipes can occur. In addition, after the pipes are placed in their final location, the backfilling process begins. During this process, backfill material is routinely dropped on top of the largely unsupported pipes during the process. The backfill then is typically shoveled and spread into place so compaction can begin. Compaction of backfill adjacent to and over pipes can result in significant loads that the pipe has to resist. Finally, even after the pipe is backfilled, it is not uncommon for heavy construction traffic to operate over the pipes before the final cover or pavement is installed. It is routine that the loads exerted by construction vehicles during site construction exceed the loads the pipes experience during the rest of their service life.
The resistance to deflection during handling and installation is where the ring stiffness of the product plays the largest role in controlling pipe deflections. Until the pipe is supported by the backfill envelope around it, the ring stiffness of the pipe is the primary means for mitigating pipe deflections.
The other significant contributor to short-term flexible pipe deflections is the consolidation of the soil envelope directly around the pipe. Even compacted backfill materials typically experience some consolidation within the first few weeks after construction. Flexible pipes simply reflect this consolidation through pipe deflection. In other words, if the soils directly adjacent to a flexible pipe move either through elastic deformation of the soil mass or consolidation of the backfill, the pipe will mirror this movement by deflecting an equal amount.
The resistance to long-term deflections in a flexible pipe is a function of both the stiffness of the soil mass around the pipe as well as the ring stiffness of the pipe itself. However, contributions in stiffness between the two elements generally are far from equal. In flexible pipe design, the stiffness of the soil embankment surrounding the pipe is far more important in controlling long-term deflections than the stiffness of the pipe itself.
To illustrate this, a widely accepted methodology for predicting long-term pipe deflections is the Iowa formula. The basis of the formula is the fairly straightforward approach that pipe deflections could be estimated by the following mathematical approach:
A modified version of the Iowa formula was developed by the U.S. Bureau of Reclamation. This modified formula appears as follows:
From the denominator of the equation, you can see that pipe stiffness is dictated primarily by the stiffness of the pipe wall (EI). The modulus of elasticity (E) is dependent upon the material that the pipe is produced from (HDPE, steel, etc.). The moment of inertia (I) is dependent on the pipe wall geometry. The soil stiffness is primarily controlled by the modulus of soil reaction (E’) of the backfill that surrounds the pipe. This modulus describes how the soil responds under load. The higher the E’ value, the more support the soil provides to the pipe to resist deflection. A representative range of E’ values for backfill materials is as follows (Figure 2):
Using this methodology, it is possible to create a comparison of estimated long-term pipe deflections for pipes with various pipe stiffnesses. Most flexible drainage pipe products have pipe stiffnesses between 5 and 75, generally varying by diameter and pipe material/construction. A comparison of estimated long-term pipe deflections based on a range of pipe-stiffness values is as shown in the following chart:
As this chart illustrates (Figure 3), pipe stiffness has greater impact on low-modulus soils than it does on relatively high-modulus soils. For a backfill material with a relatively moderate modulus of 2,000 psi, even a 15x increase in stiffness from 5 to 75 only increases the long-term pipe deflection by approximately 1%. For a 36-inch diameter pipe, that’s slightly less than 3/8 inch. Even for a very low-modulus soil, a 3x increase in pipe stiffness results in just more than the same 1% increase in pipe deflection.
Figure 3 shows that soil stiffness is the largest factor in controlling long-term pipe deflections. A pipe with a pipe stiffness of 5 will perform similarly to a pipe with a pipe stiffness of 75 in a sand backfill if the density requirements are increased from 90% to 95%. With the use of high-quality fills, the influence of pipe stiffness is almost meaningless, because the difference in performance is similar between all the pipes.
Pipe stiffness is a trait to consider when selecting a flexible pipe. The pipe needs to have enough stiffness to withstand the handling and construction loads that it will be subjected to during installation. In poorer grades of backfill, it can have some impact on the long-term deflections of the installation. However, with the use of quality backfill materials at compaction levels of 90% or greater, even a much higher pipe-stiffness pipe doesn’t have a significant performance difference when it comes to controlling long-term deflections.
Darrell Sanders, P.E., is Chief Engineer for Contech Engineered Solutions. Darrell holds a B.S. degree in Civil Engineering from the University of Cincinnati and an M.B.A. from the University of Dayton and holds a Professional Engineering license in several states. He also is a member of several industry committees, including NCSPA, AASHTO, ASTM and CSA. Darrell can be reached at dsanders@conteches.com.
Fuerst, R.P., 2013. “Method for Prediction of Flexible Pipe Deflection,” U.S. Department of the Interior Bureau of Reclamation, M-25 Second Edition.
Online quiz for this article is not active and
PDH credit is no longer available.
This article is being maintained for informational purposes only.