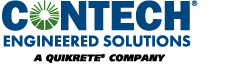
Engineered bioretention media is optimized to filter and/or infiltrate stormwater runoff through a plant-soil-microbe complex. Treatment occurs via physical, chemical and biological removal mechanisms that capture sediment, nutrients, heavy metals, bacteria, oil, grease and other constituents found in urban runoff.
Components of engineered bioretention media support both inter- and intra-storm treatment processes. Sand in the engineered media increases and maintains flow rate and provides aeration to vegetative roots. Topsoil and organic matter retain moisture, provide carbon to the microbial community, support vegetative growth and enhance pollutant removal. These components support inert and reactive filtration during storm events as well as the biological transformations and sequestration that occur between storm events. Qualifying and protecting these media components ensures the bioretention media can meet overall performance objectives.
A successful bioretention installation involves oversight—not just onsite, but having a framework in place for transferring raw materials to a blended, commercially installed product. This framework should encompass standard operating procedures (SOPs) for qualifying, sourcing, verifying, producing, storing, and handling media and media specifications to ensure recipe consistency.
Standard Operating Procedures
SOPs refer to the use of rigorous verification testing for qualifying, sourcing, verifying, producing, storing and handling media. SOPs can include internally developed procedures tailored specifically to managing media from inception to installation as well as American Society for Testing and Materials (ASTM), United States Environmental Protection Agency (USEPA) or other approved testing methods for verification testing of composition, hydraulic capacity and quality performance.
Sourcing Media
Bioretention media suppliers should follow SOPs dictating how to properly source and qualify new components to make certain the final media product performs per design specifications. In addition, where the base materials for media production are sourced should be questioned. For example, are quarry sands being mined from land historically used for agriculture or from a brownfield site? What is the feedstock source for compost? Conducting appropriate analysis of potential pollutants within the source materials is needed so issues such as leachable nutrients, metals, organics or toxic characteristics can be identified.
Considering the availability and uniformity of the materials composing the media also is important. If any of the media components are of limited supply, requalification efforts can be time consuming and result in the use of an alternative source not previously qualified due to project time constraints. Finding an available, consistent source allows for less variability in the final product and ensures alignment with product specifications.
Producing Media
If media is blended on a project-specific basis by the contractor, especially in situ, an SOP describing the process for bioretention media production is crucial. A production SOP guarantees the media and components are procured from approved suppliers, and that proper equipment and components are utilized. A production SOP should describe the components and tools necessary to manufacture media to meet specification. There should be a process providing directives on prequalification of suppliers, contact information, equipment settings, specific components, ratio of components, and reference specifications with testing SOPs accordingly.
How media is blended can vary for many reasons, including who is performing the blending and what equipment they have. Media blending is similar to how two different people following a cooking recipe may end up with a meal tasting quite different depending on the level of precision. Therefore, a production SOP alone will not always result in the same outcome, and media specifications become a critical part of the framework for media recipe consistency.
Storing and Handling Media
Storage SOPs are just as critical as blending SOPs. If bioretention media is to be stored before use, especially if stored onsite before installation, an SOP should be provided to contractors or other purchasers on how to properly store media. The main issue with media storage is cross contamination from other stored materials, tainted water and debris, especially if a site is not stabilized. Bagging or protecting media with tarps and storing on a concrete pad is ideal, as pictured below.
Media should maintain some moisture to prevent segregation of components and ensure a homogeneous blend during storage and transport. Visual differences can be seen in the same mass of media under different moisture conditions in the photo on page 5.
If media is stored as a stockpile, the supplier should periodically collect samples, following a proper sampling SOP, and samples should be tested to ensure media is within specification. Media transport has its own set of issues as well. Trucks hauling bulk media should be cleaned before use to prevent contamination from remaining residue from previous loads, and loads should be covered. In addition, each new media batch produced should receive a batch number for tracking purposes. Reference samples should be inventoried should there be any future issues requiring further testing.
Specifications, QA/QC and Certification
Media specifications, quality assurance/quality control and certification are needed to ensure recipe consistency from batch to batch.
Specifications
Although public domain bioretention design manuals will identify generic media specifications to avoid sole sourcing, media manufacturers should have very specific raw material specifications for each component within a bioretention blend to
ensure little product variation. Each time a new media batch is produced, these specifications should be followed, and analysis should be performed to confirm the media meets the specification.
Is the particle size distribution within range? What is the organic content? Is the pH appropriate? What is the composition? A product specification should also be available upon request from the media manufacturer for hydraulic and water-quality performance, and it should be questioned how these parameters were evaluated if not provided in the specification. Certification should be provided to verify proper tests and procedures were performed.
Public domain bioretention design manuals often specify ranges for media composition to include sand, topsoil, and organic matter. Phosphorus can be labile in soils under saturated phosphorus conditions, therefore measuring the soil P-Index is important in understanding the leachability of phosphorus. Leachability can be further enhanced with coarse soil texture and increased porosity. Cation exchange capacity (CEC) is sometimes specified in a media specification as well to ensure increased media reactivity for enhanced pollutant adsorption. CEC measures the amount of cations that a soil can retain, and includes measurements of calcium, magnesium, potassium, sodium, hydrogen and aluminum. CEC is driven by the amount of clay and organic material present in the soil. Media infiltration rates are also often specified, and are highly dependent upon particle size distribution and media composition. It should be noted that infiltration rates are affected by head development on the media as well as media depth, and therefore, hydraulic conductivity is a more accurate unit of measure.
QA/QC
There needs to be just as much oversight into blending the media as there is in ensuring product consistency throughout use of the media batch. Media certification must be based on high standards of quality control (QC) in bioretention media raw materials and media composition as well as use of strict quality assurance (QA) methods in the controlled manufacturing process, validated with numerous characterization, composition and performance tests conducted during and after production.
QA is process oriented and ensures the development process is adequate to ensure objectives (or, in this case, media specifications) are met, and it improves production to prevent issues later on. QC is product oriented and designed to evaluate a developed media batch to reveal product defects.
So why do we need media QA/QC? QA/QC procedures are critical to ensuring the media functions as designed. Is the media outside spec, and, if so, is it due to media production, storage or other issues? Bioretention media is a natural product with product variations, thereby requiring more QA/QC than a more consistent or synthetic product may require. For example, the same sand product can have natural variations at a quarry depending on the mining location and depth.
Different methods of blending can be used by different suppliers, leading to a different final product. Various QA tests should be conducted to ensure the blending equipment is effective and properly calibrated to meet the media specification. Also, directions can get lost in translation and, therefore, strict oversight of new suppliers is critical. Sometimes media substitutions are made to meet project deadlines or simply because contractors often do not understand the technical nature of the product and haven’t been properly trained.
Additionally, there needs to be more emphasis on source qualification. Verification testing alleviates many of the issues observed with public-domain bioretention systems. Verification testing should be performed via relevant ASTM, USEPA or other standards. Excessive nutrient leaching due to high P-index materials or nutrient and/or metals leaching due to unqualified compost can occur without proper testing to evaluate the composition of materials in a bioretention blend.
Post-Construction Verification
Post-construct verification is highly recommended to confirm hydraulic capacity was not compromised during construction. In-situ flow-rate verification should be conducted at several locations across the bioretention media surface area. The verification methodology should measure hydraulic conductivity rather than infiltration rate alone.
Measuring infiltration rate only confirms the rate that runoff enters the bioretention media at the surface, providing results unrepresentative of underlying soil conditions. Infiltration rates are affected by head development on the media as well as media depth and various physical characteristics such as soil structure, compaction, bulk density, organic matter, antecedent moisture conditions, etc., and therefore, calculating hydraulic conductivity via Darcy’s Law is a more accurate unit of measure. Initial rates of infiltration into dry surface soils can be quite rapid, and then will decrease as the soil wets and/or swells. The figure below demonstrates this concept through example infiltration rate curves utilizing the Green-Ampt model to compare dry bioretention media versus saturated bioretention media. The Green-Ampt model recognizes the existence of a wetting front and the soil suction head at that wetting front as well as soil porosity, hydraulic conductivity and time. Assuming constant head conditions, the infiltration rate will equilibrate and reach an asymptote after some period of time, providing a more accurate representation of bioretention media hydraulic characteristics. Therefore, bioretention media flow tests should be measured as a hydraulic conductivity under saturated soil conditions.
For slow-flow bioretention media, double-ring infiltrometers often suffice. High-flow bioretention media require a larger testing apparatus to enable a greater volume of water to be introduced to capture higher flow rates as pictured below. It is recommended that the entire media profile depth be tested under saturated conditions to ensure the flow rate is at capacity throughout the media bed, and the underdrain functions as designed. Testing under saturated conditions allows for data collection representative of worst-case conditions. Infiltrometers are useful not only during initial verification of design specification, but also to quantify maintenance needs as part of a predictive maintenance program.
Certification
When proof of media certification is requested, a media batch certificate should be provided. The certificate should certify hydraulic and pollutant removal performance as well as that the media composition meets the specification per QC verification testing. If the media is being provided to meet a design manual specification, the certificate should reference the requirements within the media specification. Media batch numbers should be referenced in the certificate to know the certification is relevant to current inventory and can be referenced. Historical certifications should be filed as media batches are produced should a future issue arise.
A successful bioretention media installation must have a framework in place for transferring raw materials to a blended, commercially installed product. Although this in itself is quite a feat, as there are a number of variables that can contribute to media failure, proper design and installation are equally important for ensuring operational success. By following the appropriate framework for a media certification test program, the stormwater designer can be confident that use of media in his or her bioretention plan will yield the same performance as specified in the bioretention design manual.
Online quiz for this article is not active and
PDH credit is no longer available.
This article is being maintained for informational purposes only.