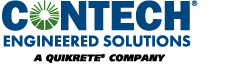
The types of acceptable granular backfill material suitable for use with flexible soil-interaction structures are well-documented and described in industrial standards. These documents include: product-specific ASTM standards, American Association of State Highway and Transportation Officials (AASHTO) Bridge Construction Specifications, installation manuals published by the National Corrugated Steel Pipe Association (NCSPA) and American Water Works Association (AWWA) and many Federal Highway Administration (FHWA), state department of transportation, county, and municipal standard specifications. In general, any well-graded granular material that is suitable for use for construction of a quality road base will meet industry standards. For the purpose of this article, granular materials that are found onsite are called "soil" and manufactured granular materials are called "aggregate."
Granular soil found on a particular project site may be appropriate for use as backfill in accordance with project specifications. Such soil is typically a mixture of granular particles with silt and clay. The most commonly specified sizes range from a maximum of 3 inches to the standard No. 200 sieve particle size (visible to the naked eye). Using the Unified Soil Classification system, well-graded soils classified as GW, SW, GM, SM, GC, or SC that are primarily non-plastic are generally acceptable for backfilling flexible structures. However, ML and CL materials, which are primarily silt and clay, should be avoided.
It is the responsibility of the engineer of record to specify appropriate soil characteristics that provide adequate structural support. If borrow material that meets project specifications is not available, it may be necessary to import select aggregate fill material. Aggregate can originate from either a natural source (sand and gravel pit) or be a manufactured aggregate from a quarry.
The following characteristics are common to all suitable granular backfill:
Suitable backfill materials normally are available from prequalified manufactured sources or borrow pits and should be used whenever possible. A qualified local geotechnical engineer or construction materials testing laboratory should assist with evaluating backfill sources. This is especially important when considering onsite borrow pits.
Test | Description | AASHTO Specification |
pH | Determine if the material is neutral, acidic, or caustic | T-288 |
Resistivity | Indicates potential for a material to facilitate corrosion; indicates presence of dissolved salts |
T-289 |
Gradation on a received sample |
Indicates particle size distribution; determines maximum size and minimum size |
T-27 |
Proctor | Determination of material moisture-density relationship (applies to gradations that mimic road base materials; does not apply to coarse aggregate with few fines) |
T-99 or T-180 |
Density | Unit weight and voids | T-19 |
Los Angeles Abrasion and Impact test | Determines soundness and resistance to degradation under backfill placement and compaction forces | T-96 |
Gradation on sample after Los Angeles Abrasion and Impact | Indicates presence of excessive fines after application of compaction equipment forces | T-27 |
Total dissolved sulfates |
Indicates presence of corrosive salts | T-290 |
Total dissolved chlorides |
Indicates presence of corrosive salts | T-291 |
All recycled materials served a purpose prior to their new intended use as select backfill material. Because the composition and previous service environment of these recycled materials may not be known, it is important to qualify the proposed recycled aggregate prior to allowing its use as backfill.
The tests listed in Table 1 should be performed to assess if a recycled material should be considered for use.
AASHTO M 319 further cautions the engineer to consider compaction and consolidation relative to moisture content and repetitive live loads, potential leaching of highly alkaline minerals and soluble calcium salts and minerals into groundwater, potential changes in permeability over time, potential changes in soundness over time, and possible contamination with extraneous solid waste or hazardous materials.
Recycled portland cement concrete is produced from crushed concrete that has been removed from service. The material contains the sand, rock, and cement binder that was used in the original mixture along with any additives (chemical admixtures or cement pozzolans) used to control setting time, placement, or durability. The most common source for recycled concrete is pavement or portions of ready-mix deliveries that are returned to the plant. Foreign material such as pieces of rebar and steel mesh and any organic or deleterious substances should be removed. Recycled concrete that meets the above physical and chemical testing requirements and procedures should be acceptable for use as backfill with flexible structures.
Other recycled aggregate/binder combinations such as brick and lime mortar or structural repair mortars that use pea gravel and magnesium phosphate, epoxy, or polyurethane binder should be avoided. Recycled concrete that contains appreciable concentrations of road de-icing salts may not be suitable because of the potential corrosive nature of these salts and potential damage and deterioration concerns for the new structure.
Recycled asphaltic concrete (AC, bitumen, macadam, or simply asphalt) is also used for roadway surfaces. Aggregate particles are bound together with a distilled product of crude oil under heat and pressure. Asphalt is typically 95 percent aggregate and 5 percent asphaltic binder. However, the 5 percent binder significantly influences the overall behavior of the mixture. Asphalt behaves like a very thick liquid similar to soft clay. As such, it is somewhat elastic in nature. In general, because of the potential for such materials to compress under loads, all types of asphalt should be avoided for use as backfill material around flexible structures.
Slag is a byproduct of the blast oven steel-making process and is readily available in areas with close proximity to steel mills. Slag is typically a sound material with good physical properties, but the chemical composition of slag should be checked carefully prior to acceptance. The potential exists for corrosion issues related to such chemicals in close proximity to certain structures, as well as the potential for detrimental environmental effects.
Foundry sand is used in metal forging production and is readily available as a surplus or spent material. The gradation of foundry sand is specific to the metal forging process and should be evaluated carefully before such material is considered for use as backfill. Also, the presence of unwanted metal or chemical compounds should be determined prior to use.
Bottom ash and boiler slag are the waste materials that are collected in the lower systems of industrial furnaces. Bottom ash and boiler slag materials, unlike fly ash, are generally much larger in particle size, being generally in the 1/2-inch to sand size range. These materials typically have a single particle size (poorly graded), have potentially high sulfate and iron contents, and tend to be of relatively low density and may be prone to degradation during accepted hardness tests such as the Los Angeles Abrasion test.
At some sites, the use of self-compacting materials has proven to be beneficial in providing adequate support to flexible structures, especially in tight spaces where placement and compaction of more traditional backfill material would be problematic. Challenging situations such as placing bedding under haunches, backfilling between closely spaced parallel structures, or installing structures that are partially submerged can be simplified or enhanced by using self-compacting materials. The most common materials used are either open-graded, angular aggregates or specially proportioned cementitious mixtures.
Open-graded stone (OGS) is a common name for a granular aggregate whose particles are primarily one size. The most common OGS sizes are 3/4 inch and 3/8 inch. These sizes of coarse aggregate typically are used for concrete and mortar production and also in conjunction with perforated drainage pipe to construct perimeter drains (French drains). It may be possible to obtain satisfactory results when constructing subdrain systems using small-diameter pipe by dumping fill in place in a controlled manner. However, for pipe diameters greater than 48 inches, it is recommended that the fill must be placed in controlled, balanced lifts no larger than 8 to 12 inches.
The larger 3/4-inch material is commonly supplied as crushed limestone and is typically angular in particle shape, which promotes the interlocking of particles and helps to confine the pipe walls. The smaller 3/8-inch material is commonly supplied as rounded or irregularly shaped particles, frequently referred to as "pea gravel." Such fill material needs to be worked in carefully under the "haunches" of the pipe to ensure adequate coverage and support. Because the size of pea gravel coincides with the diameter of some standard perforations, the selection of this size material should be considered carefully when used for installing perforated pipe systems. A common practice is to wrap perforated pipe with a nonwoven geotextile to guard against infiltration of backfill material into the pipe system. OGS typically has a void content of as much as 40 percent. The voids in the backfill can be considered as part of stormwater retention, recharge, or percolation systems to help store and then release captured rainwater back into the ground. Because the OGS also must provide soil-interaction support to the pipe, the placement of such fill is critical. Unfortunately, in-place density testing of OGS is not universally accepted and can be impractical. The in-place density of such materials often can be enhanced using compaction devices such as plate compactors and concrete vibration tools. Verification of thorough placement coverage of this fill material combined with ensuring sufficient density to support the pipe system adequately and to carry any applied surface loads is critical. Consequently, the installation quality often is dependent on a combination of site conditions, material choice, and installer experience.
It also is likely that there will be a significant difference in gradation between OGS and the adjacent native soils. It is common practice to place a non-woven geotextile separator between the differing soils to prevent migration of fines and filling of voids.
A common mistake is to assume that the use of an OGS is necessary to satisfy the requirement for freedraining backfill. Most well-graded granular backfill materials have adequate porosity to allow water to drain. A granular backfill will drain more freely than a cohesive, clay backfill, which is one reason cohesive fill materials are not recommended for use as select backfill for these pipe systems.
Controlled low-strength material (CLSM, also known as flowable fill or controlled density fill) is a mixture of sand, cement, water, and fly ash. Fly ash is a major component of CLSM and is a byproduct of burning coal for generating electricity. Fly ash is a finely ground waste material that is captured in the exhaust stacks prior to release into the atmosphere. The chemical composition of fly ash varies based on the source of the burned coal. Similar to freshly placed concrete, CLSM can have a high pH in excess of 12. Also, the mixture should be evaluated for the presence of cure time accelerators such as calcium chloride, which potentially can be corrosive.
When using CLSM, the requirement for free-draining backfill commonly is waived as the lack of porosity is compensated by the stiffness and strength of the hardened CLSM and its resistance to swelling as moisture content changes. CLSM can have a relatively low density and can be somewhat buoyant in nature, so lift thickness must be staged carefully so that structures with full inverts are not floated off the bedding. In addition, such materials must be placed in a relatively balanced and controlled manner to avoid distortion or displacement of the pipe structure.
In geographical areas where coarse-grained soils and aggregate are not available or feasible, the use of soil-cement mixes are common to help stiffen and strengthen available soils. Local construction specifications and practices should be used in these geographical areas. In general, a good understanding of the optimum moisture-density relationship of the soil with and without blended cement is necessary.
There are many possible materials that can be considered for use as backfill material for flexible soil-interaction structures. Determining whether a material is suitable for use on a particular application depends on a number of practical and site-specific considerations and factors. The reader is encouraged to understand the important and sometimes not immediately obvious characteristics and key differences in such materials prior to selecting backfill for a particular site application. Factors such as required support, site constraints, project location and proximity to select fill sources, relative economics associated with material cost, backfill placement, and compaction costs all enter into the decision process. This article identifies and evaluates a number of the relevant factors; however, when in doubt, employ the services of a well-qualified and experienced geotechnical engineer.
Steve Tysl, P.E., is a product design engineer for CONTECH. He has more than 20 years of experience in civil and materials/construction engineering. He is a member of ASTM, SEAoO, and NCSEA.
Jim Noll, P.E., is director of engineering services for CONTECH. He has 35 years of experience in the corrugated metal pipe industry and is an active member of various technical organizations including ASCE, AREMA, NCSPA, and ASTM.
Online quiz for this article is not active and
PDH credit is no longer available.
This article is being maintained for informational purposes only.