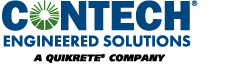
Pipe joining systems vary widely across the range of pipe systems used in the United States. In general, pipe joints are designed to match the performance and testing standards required for the application in which they are to be used.
The purpose of this article is to correlate some of the most common pipe joining systems currently in use and highlight some of the performance and testing standards used in specifying joint requirements for each application.
The applications discussed in this article are as follows:
Other applications that require pipe and pipe-joining systems are beyond the scope of this article.
The American Association of State Highway and Transportation Officials (AASHTO) recently identified four levels of joint performance and described each level as follows:
Soil tight joint — Soil tight joints are specified as a function of opening size (maximum dimension normal to the direction that soil may infiltrate), channel length (length of the path along which the soil may infiltrate), and backfill particle size. If the size of the opening exceeds 1/8 inch, the length of the channel must be at least four times the size of the opening. No opening may exceed 1 inch.
Silt tight joint — A silt tight joint is resistant to infiltration of particles that pass the No. 200 sieve. Silt tight joints are specified to provide protection against infiltration of backfill material containing a high percentage of fines, and typically utilize some type of filtering or sealing component, such as an elastomeric rubber seal or geotextile wrap. Geotextile wraps are manufactured to tolerances that ensure silt will not pass through them. The successful performance of these wraps in the field is dependent on their installation. If a geotextile wrap is specified for use, the material specified should meet AASHTO M288, with an Apparent Opening Size (AOS) greater than 70.
Leak resistant joint — A leak resistant joint is specified when water leakage into or out of the pipeline system is a concern. Leak resistant joints limit water leakage at a maximum rate of 200 gallons/inch-diameter/mile/day for a specified head or pressure.
Special design joint — Special design joints are joints requiring special strength in bending or shear, pull apart capabilities, or unusual features such as restrained joints placed on severe slopes, welded joints, and flanged and bolted joints for high pressures, high heads, and/or velocities. These joints are typically described within the special provisions of the project specifications. Water tight joints that provide zero leakage for a specified head or pressure application are included in this category.
Culverts — Typically, the primary consideration for pipe joint performance on culvert installations is only to prevent the loss of backfill materials through the joints. A loss of backfill through the joint can lead to voids within the embankment. This can potentially impair performance of the embankment or can lead to a loss of support and stability for the pipe itself. Generally, a soil tight joint can be used successfully in these applications. However, for installations that use unbound backfill materials with a high percentage of fine-grained soils, a silt tight joint is likely more appropriate.
Underground detention/retention systems — Detention or retention systems are generally constructed using a series of interconnected vaults or large-diameter pipes to save land area by storing stormwater runoff underground (see Figure 1). Unlike recharge systems, which typically utilize perforated pipe or open-bottom chambers to infiltrate runoff underground, temporary detention and permanent storage systems are generally designed to hold and store surface runoff. Detention systems typically store runoff on-site temporarily during a storm event and release the water in a slow, controlled manner to lessen the impact of runoff from a particular site. This ensures that the hydraulic systems downstream of the site are not overburdened by the runoff from the storm event.
In these systems, some leakage from the pipe joints is typically not an issue and soil and silt tight joints are all that is commonly required. Exceptions to this could include situations where specifiers or agencies are concerned with the potential leaching of pollutants from the surface runoff through the pipe joints, or sites in which the soil around the detention system cannot be saturated, generally because of the need to maintain a consistent bearing capacity within the soil mass. In these exceptional cases, a leak resistant or water tight joint will likely be required. Many sites utilize separation devices upstream of detention and filtration devices downstream of detention to create a complete stormwater system with pretreatment, storage, and final treatment. Permanent storage systems are becoming more popular as more individuals and agencies recognize the benefits of storing and reusing stored surface water for irrigation, fire water systems, or other uses. These systems are generally designed to be water tight.Storm sewers — This category of installations probably has the widest range of joint performance requirements of any that will be discussed in this article. Storm sewer systems simply capture and carry the surface stormwater from a site to a channel, stream, or lake. Traditionally, these systems were treated like culvert installations in that they only required a soil or silt tight joint, depending on the gradation of the native soils in which the system was being installed.
However, as discussed regarding underground detention systems, many agencies now require a higher level of joint performance to limit exfiltration of pollutants from the storm sewer system into the surrounding soils. Additionally, as with the detention systems, many agencies are now installing filtration or separation units into storm sewers to capture and remove pollutants before they are discharged. Frequently, if water tight joints are required, in-field testing will be performed to ensure the joint integrity for the system. This in-field testing typically begins by isolating pipe runs between manhole structures with pipe plugs or inflated bags. The pipe run is then filled with low-pressure air or water and any leakage is measured. Most specifications allow for a limited amount of leakage over a specified period of time.
Sanitary sewers — Virtually all sanitary sewers require water tight joints and are field-tested to ensure joint performance (see Figure 2). The effluent captured in these sanitary installations contains many pollutants and needs to be contained within the sanitary system until it can be carried to a treatment facility. Most sanitary sewers are designed to perform under gravity flow and can be subjected to intermittent pressure for short periods of time, but are not designed for use under constant pressure. Sanitary installations are routinely deeper than storm sewer installations and therefore are more likely to be subjected to the potential for groundwater infiltration through the joints and into the system. Field testing is required to ensure that all of these requirements are addressed in the system as installed.Irrigation systems — The demands on irrigation systems have the greatest variation in the required performance of the system. While most irrigation systems operate under pressure, the magnitude of the pressure can vary from 3-5 pounds per square inch (psi) to 100 psi or more due primarily to the surface terrain and elevations within the system. Many of the higher-performance systems require either mechanical joints to hold the pipe ends together or fusion welded joints. As would be expected, the primary concern with these systems is leakage of the irrigation water out of the pipe.
Corrugated metal pipe
External band, with or without a gasket — This is the most common form of corrugated metal pipe band. It consists of a smooth or corrugated external sleeve that generally indexes with pipe corrugations to provide some mechanical interlock between the band and the pipe (see Figure 3). Without gaskets, this is an effective soil tight joint. With the addition of gaskets and possibly other features such as rods, lugs, et cetera, this joining system can provide varying degrees of water tight performance. Pipes with this joint are typically used in culvert, detention/ retention, and storm sewer applications.
Plastic pipe
Split couplers — These are an inexpensive pipe joining system used primarily in culvert, detention/retention, and storm drainage applications and are typically only used on profile wall pipes. The joint is typically constructed by expanding a slightly oversized shell of the pipe profile to fit over each end of the pipes to be joined. The coupler indexes the profile and is held in place by straps, zip ties, or some other means of securing the edges of the shell together.
Bell and spigot joint — This is the most common joint used to join plastic pipes. Its construction consists of a smooth-walled bell that is sized to accept a gasketed pipe spigot. The gasket is compressed between the outer wall of the spigot and the inner wall of the bell to form the seal between the two pipes (see Figure 4). Bell and spigot joints are used in culvert, detention/retention recharge systems, storm and sanitary systems, and low-head irrigation applications. Varying levels of performance are achieved through the amount of compression placed on the gasket and the construction of the bell and spigot to be able to maintain the compression load on the gasket over time. To achieve and maintain water tight performance, the construction of the bell and spigot are important. Compression of the gasket can be lost due to creep in the material from which the parts are constructed. This could lead to a loss of water tight performance over time if it is not addressed through reinforcement of the bell and spigot with materials that will limit the long term shape change within the joint parts.
Concrete pipe
Tongue and groove joint — This joint typically consists of a tongue and groove fabricated on matching pipe ends to provide some indexing when the two pipe ends are assembled. The void between the surfaces within the joint is typically filled with a mastic joint compound or mortar (see Figure 5). This joint is typically used in nonpressure applications such as culverts, most detention/ retention systems, and some storm sewer systems.
Bell and spigot joint — These joints have external shoulders formed in one pipe end to form the bell. The spigot is generally formed with a notch to accept an o-ring or other rubber gasket (see Figure 6). These joints are generally considered water tight for low-head applications and are frequently used in culvert, detention/retention, storm and sanitary systems, and low-head irrigation systems.
To logically specify the type of pipe and the required joining system for a given pipe system application, it is essential to understand the performance differences and features of the pipe products being considered for use, along with the details of the various joining systems that are available. Issues to be considered include the relative leakage resistance characteristics of the joints and connections as related to the site conditions. Criteria such as the need for joints that are soil tight versus silt tight versus leak resistant should be part of the decision process. The strength of the joining system in situations requiring special connections because of bending, shear, or pull-apart scenarios could also be a key consideration.
A related concern is the need for the pipe system joints to provide initial or short-term performance, along with long-term performance capabilities that will serve the expected life of the project. Quality joining systems that must provide long-term performance in real-world environments should employ suitable details — such as reinforced bell and spigot ends — to limit shape change that could result in reduced performance with time.
Specifying a suitable pipe product and selection of the appropriate joining system — combined with proper installation — will result in a satisfactory pipe system that meets the needs and performance requirements of the project.
Online quiz for this article is not active and
PDH credit is no longer available.
This article is being maintained for informational purposes only.