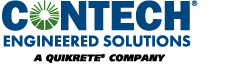
Changes in traditional stormwater management practices are underway and regulatory agencies are implementing new guidance and requirements for Low Impact Development (LID). The new rules focus on runoff reduction strategies including reduced impervious area and onsite infiltration. These options can be challenging to implement and are not practical in every situation. Engineers, architects, and developers are designing rainwater harvesting (RWH) systems as an alternative LID practice to keep water onsite and reduce runoff. Compliance with runoff reduction requirements is a compelling economic benefit for developers to justify a RWH system that would otherwise be eliminated from consideration despite the environmental benefits. With the runoff reduction benefit as the primary justification, the project may capture the additional benefits of LEED points, reduced utility bills, and lower demand on municipal water systems.
RWH does not have a long history of use in modern site design, but now that it is a topic of interest, many engineers and architects need to learn this multi-faceted new practice. A previous CE News Professional Development Series article discussed overall system components and general design requirements. This article focuses on the most central — and in many cases the most costly — component in the system: the cistern.
Cisterns are available in all shapes and sizes, but there are basic attributes that should be present in every cistern no matter what type is selected (see Figure 1). The most common elements to specify include the following:
Watertight rating — Vessels designed to hold water should be able to maintain a minimal watertight rating for the life of the cistern. Since almost all systems are open to the atmosphere, this is usually passive head pressure equal to the depth. In most cases, it is only a few pounds per square inch (psi). Tall, aboveground cisterns are the exception where 10-15 psi may be more common. Testing to ensure the watertight rating can be difficult for large systems, so a factory test or production standard may be the best specification requirements to ensure water tightness of the delivered system.
Code requirements — Many state plumbing codes require two important elements in a cistern that are designed to improve water quality. The first is a calming inlet, which creates full pipe flow within the inlet pipe and discharges influent water upward from the bottom of the cistern. This reduces turbulence and the potential for disturbing solids that have settled on the bottom of the cistern. The second common requirement is a floating outlet. The intake hose to the pump should be flexible with an attached inlet screen to block gross pollutants. The hose should be connected to a float so that the intake is never at the very bottom of the tank where solids could be sucked into the pump. It should also never be at the surface where fine floating materials may be present. The float should be suspended within the water column, ensuring the cleanest water within the cistern is extracted. This improves the quality of the re-use water. Cisterns should also have an overflow path, vents and screens or water traps over the inlets and outlets to prevent access by insects and animals.
Pump types and location — There are many options to configure pumps. Submersible pumps placed directly in the cistern or in a downstream wet well are powerful options for applications with higher head, but must be hard wired with power into the cistern. Suction pumps placed aboveground are also common, but are limited by depth and pressure. In many cases, a low-pressure transfer suction pump is connected to the cistern with an additional pressure booster pump in the mechanical system.
Access and maintenance — RWH systems may have a design life of 20 to 50 years or even longer. Even though all systems should include pretreatment, sediment will collect over the years as millions of gallons of water pass through a commercial-sized system. All cisterns should be designed with multiple access points to support pump maintenance, inspection, repair, and cleaning.
Cistern placement is a trade-off decision unique to every site, and there are many pros and cons of aboveground and belowground configurations.
Aboveground systems can be an attractive design element for a project and do not require excavation. They are typically limited in size to 10,000 to 15,000 gallons unless there is space for a large footprint or multiple cisterns. They may also need to be taken offline in cold weather climates, or heaters can be added in milder climates with infrequent cold snaps. In many jurisdictions, cisterns greater than 5,000 gallons will need a structural design and foundation that accounts for wind and seismic loading. Despite these design challenges, nothing makes a statement about water consciousness like an aboveground cistern.
Belowground systems save valuable land space, are protected from cold weather, and can be almost limitless in size. While they do require excavation — which may increase installation cost — the material cost is usually lower per gallon for larger systems. Most commercial projects utilize a belowground option.
There are a wide variety of cistern materials to choose from (see Table 1). Because they are often smaller in size, residential systems offer more options, but not all will scale to tens of thousands of gallons in a cost-effective manner. This article focuses on commercial- and institutional-scale projects where storage requirements are thousands of gallons and larger.
Fiberglass tanks are a common choice for RWH tanks because they offer high pressure ratings and resist corrosion. They are mostly used belowground and can be sized up to 60,000 gallons and 12 feet in diameter. While long lasting, they are often not the most economical choice and require special care during handling and installation. Because they are built as continuous tanks, the large sizes require over-sized shipping loads that increase overall costs. Multiple tanks are required for large systems.
Polyethylene tanks can be used for underground cisterns and can be a very affordable choice for small systems less than 3,500 gallons. They are lightweight, easy to transport, and easy to handle at the jobsite. They may be difficult to implement on many sites because they require significant cover, but are limited in depth, which means there is a narrow range where the inlet pipe can be located. Many tanks must be connected together to create even mediumsize systems, which can offset cost savings.
Steel Reinforced Polyethylene (SRPE) cisterns are newer to the market and combine the longevity of polyethylene and the strength of steel in an efficient and economical package. These tanks resist corrosion and can last longer than 75 years. Sections are manufactured as long as 50 feet and multiple sections can be combined and fused together in the field to create one large, leak-proof cistern sealed to a 15 psi rating. SRPE is easily patched in the field if damaged and can handle burial as deep as 30 feet. For cisterns larger than 20,000 to 30,000 gallons, they can also be the lowest cost option (see Figure 2).
Plastic crates were once used solely for infiltration, but with a waterproof liner, they are also an entry level cistern option. The liner is installed prior to the crates. Because liners can be prone to damage and installation errors, they often have a much shorter lifespan than other cistern options. They are an economical solution for sites requiring large storage volumes because they do not require heavy equipment for installation. More economical crates are typically not strong enough for more than 6 feet of cover, so increased cover will increase cost. There is no maintenance access, so the design life for these systems could be less than 20 years.
Concrete structures can also be used as cisterns. They can be precast for faster installation or cast-in-place to suite specific site constraints. To achieve a watertight system, special care must be used to seal joints, and the engineer should require a coating appropriate for re-use applications because people and the environment will come in contact with the water. Concrete can develop leaks over time from cracks, and — in most cases — will need to be drained to seal the leak. For small- to medium size systems, concrete can be a more expensive option. But for very large systems, concrete structures may offer a better economic value and are worth consideration where the cistern will be under high loads.
Fabricated steel tanks are another common option to store fluids and can be extremely strong, with a design life of 50 years or more in the right conditions. They can be painted or coated to increase their life, but can be very expensive and also limited in size.
Waterproof corrugated metal cisterns are another newer option for water storage. Thin gage steel with an aluminum alloy coating offers a cost-effective system, and can have a design life greater than 75 years in many conditions. These lightweight tanks can be built in diameters up to 12 feet and up to 50 feet long. Because these tanks are newer on the market, engineers should require testing documentation from a reputable supplier before specification. For small- and medium-size systems, these are the most economical option in most situations.
Aboveground metal cisterns are the most common aboveground option and employ thinner gage steel for the structure and an impermeable liner for containment. There are two types of systems: curved plates assembled onsite and monolithic set-in-place designs. Tanks that are built onsite can be larger in diameter, but it may take days to assemble the steel panels and fasten thousands of bolts. Monolithic cisterns can be as large as 15 feet in diameter. Because they arrive completely assembled, installation can be completed in a matter of hours. Either type can last 75 years or longer because the aboveground environment can be less corrosive than underground.
Sizing a cistern to meet LID rules is challenging because most jurisdictions provide limited guidance, and existing tools do not yet include RWH. Sizing is best done with a continuous daily simulation model that calculates runoff captured, overflow and runoff released, domestic water savings, and required makeup water. While this topic warrants its own discussion in a separate article, there are basic relationships that are important to understand. There is a limit to the percentage of runoff reduction RWH can achieve. For sites where annual re-use demand is less than annual runoff, the runoff reduction limit is simply the re-use demand divided by the annual runoff volume. No matter how big the cistern is, this threshold cannot be surpassed. Even for sites where re-use demand is greater than the annual runoff volume, increasing cistern size offers diminishing returns because of the seasonality of rainfall in most locations. It is usually better to include more re-use applications to increase re-use demand than to increase cistern size beyond standard water quality volumes typically in place today.
Design life is an important design consideration and different material types offer a wide range of life expectancy. Similar to detention systems, it is imperative to select a material that will last in the local conditions for the life of the project, which can be many decades. Unlike detention systems where the primary concern is the structural integrity, cisterns must also remain watertight during their life. For example, systems depending on liners may have a significantly shorter design life because they may be prone to leakage and cannot be repaired. While underground metal cisterns can have a design life of more than 50 years in many situations, some sites have soils that can be corrosive to metals. Other materials may be better suited for these situations. Ultimately, the best solution is dependent on the desired design life and the local soil conditions.
Structural capacity is a crucial factor when selecting a cistern. For commercial-scale systems, cisterns can be large, like detention systems, and many times the obvious choice is to install beneath a parking lot. Some of the smaller, entry level cisterns have limited loading capacity, so it may be better to locate them in a green space. For project sites that experience seasonal high groundwater, the cistern manufacturer should supply buoyancy calculations. Most cisterns can be equipped with antibuoyancy devices that prevent floating. Cisterns built from crates should be avoided in this situation because they cannot be strapped down effectively.
Installation and handling can be an overlooked design factor when choosing a cistern. Many materials — such as fiberglass — require stone backfill and are not strong enough to be backfilled with native soil. For large systems, these costs can add up. For other materials such as SRPE, depending on the quality of the native soil, it may be possible to use a competent native material as backfill for the cistern. Using local materials as backfill can save the cost of exporting excavated soils and importing expensive stone. In addition, some materials must be handled with care and have a low impact resistance; bumps and dings sustained during unloading and installation can be costly to repair and upset project schedules.
All stormwater systems need to be maintained to continue operating effectively, and RWH is no exception. Unfortunately, many owners today do not care that their stormwater BMP is not functioning due to lack of maintenance. What is unique about RWH and cisterns is that owners depend on their continued operation and associated utility savings. Easy access and maintenance is more important for cisterns and RWH systems than other LID practices.
During the first year, quarterly inspections are recommended to assess site loading and verify initial operation. After that, annual inspections should be sufficient. The inspection process is simple: Check the inlet, floating outlet, and overflow for blockages and the amount of accumulated sediment. A drainage area of one acre will generate almost 1 million gallons of runoff annually (in areas with 36 inches of rainfall). Over many years, the runoff will carry a significant sediment load despite pretreatment, and eventually accumulated sediment should be removed.
Maintenance cycles are five to 10 years or longer in most cases. It is important for engineers to design access points for cleaning, inspection, and repair to ensure the owners benefit from the RWH system for the full life of the system.
Closed systems that do not allow access can severely limit the ability to do maintenance or repairs and a small installation error or internal blockage can be extremely costly or render the system obsolete. Open and accessible systems ensure successful operation of the cistern for the full design life.
Greg Kowalsky, BSME, is the Low Impact Development product manager for CONTECH Construction Products Inc. He is an active member of the American Rainwater Catchment Systems Association (ARCSA) and has six years of experience in stormwater design and 15 years of engineering experience.
Kathryn Thomason, P.E., is a senior design engineer with CONTECH and currently specializes in stormwater treatment, detention, and rainwater harvesting design.
Online quiz for this article is not active and
PDH credit is no longer available.
This article is being maintained for informational purposes only.