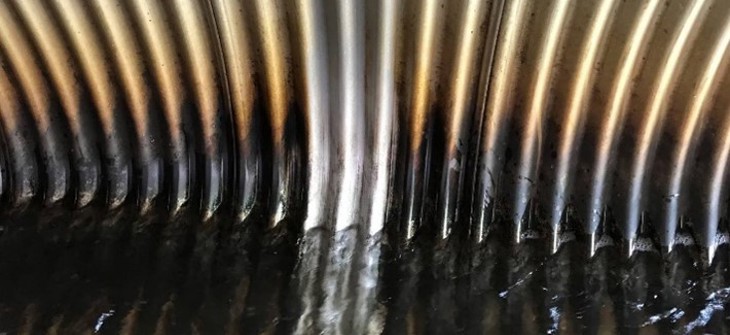
Why Aluminized is better than Galvanized for Culvert Service Life
Metallic Coatings History
Metallic coatings have been applied to iron and steel armaments as early as the 17th century. The purpose of metallic coatings applied to steel is to help retard corrosion. The zinc coating process of steel, referred to as galvanizing, was named after Luigi Galvani, an Italian physicist who lived in the 18th century. Galvanized steel in the construction industry came into widespread use in the early 20th century. Today there are two prominent metallic coatings for corrugated steel pipe, zinc coated (galvanized) meeting AASHTO M218 and aluminum coated (aluminized) meeting AASHTO M274. Galvanized corrugated steel pipe was first installed in the US in 1904, and aluminized was first installed in 1952. Both galvanized and aluminized coatings require a scale barrier formation to protect steel.
Zinc versus Aluminum Coatings
Inherently, zinc coatings (galvanized) are corrodible in water and wetter soils. Fortunately, in hard water environments, galvanized performs well because corrosion is retarded by the formation of protective-barrier scales, produced mainly by deposits of calcium and magnesium minerals.
Zinc corrosion products contribute to scale formation. Durability problems, which sometimes arise, are associated with conditions that hinder barrier-scale development. These can include softer non-scaling waters, water or soil with excessive amounts of corrosion-accelerating salts, turbulent waters, and abrasive bed loads.
Aluminum coatings (Aluminized Steel) are more durable than zinc coatings. This is due to the formation of an aluminum oxide film which is more protective than the mineral scale on zinc. The film forms in both hard and soft water and is resistance to corrosion by Sodium Sulfate (S04-2), Nitride (N3-), Carbon Dioxide (CO2), and Oxygen (O2) and organic acids.
The film also is resistant to erosion by turbulent water. Additionally, if the film is damaged or removed by intermittent hard abrasive or chemical influences, it is immediately reformed after the disappearance of these influences.
The aluminized coating is a two-layer, metallurgically bonded composite with advantageous composite corrosion behavior. It consists of a protective layer of aluminum and an underlying layer of aluminum/iron alloy. The alloy possesses high corrosion resistance and acts as a second line of defense against general corrosion in addition to acting as a pit arrestor.
The FHWA Report RD-97-149, Durability Analysis of Aluminized Type 2 Corrugated Metal Pipe, concludes Aluminized pipe will provide 3.5 times the service life of galvanized pipe.
Aluminized Steel – Protective Dark Scale from Alloy Layer
![]() |
![]() |
MT Highway 287, Norris, Montana – Installed 1987 (37 years in service)
Above right: Taking measurements of 112” X 72” Aluminized Steel Pipe Arch Culvert
Above left: Heavy protective dark scale (stain) wiped away to show shiny metallic coating. The aluminized culvert is in excellent condition with turbulent water flow.